Advanced Welding WPS: Customizing Specs for Complicated Projects
Advanced Welding WPS: Customizing Specs for Complicated Projects
Blog Article
Understanding Welding WPS Standards: Ideal Practices and Techniques for Quality Welds
In the world of welding, grasping Welding Procedure Requirements (WPS) requirements is an important component that straight influences the quality and stability of welds. As we navigate via the details of welding WPS criteria, discovering vital insights and approaches for achieving top-tier welds will certainly be critical for welders seeking to excel in their craft and create welds that stand the examination of time.
Understanding Welding WPS Specifications

Comprehending WPS requirements is vital for welders, designers, and inspectors included in welding procedures. By complying with WPS standards, welders can produce welds that meet the called for mechanical buildings and structural honesty. Examiners depend on WPS documents to validate that welding procedures are being adhered to correctly and that the resulting welds are of premium quality. Designers use WPS criteria to design welding procedures that make certain the sturdiness and integrity of bonded structures.
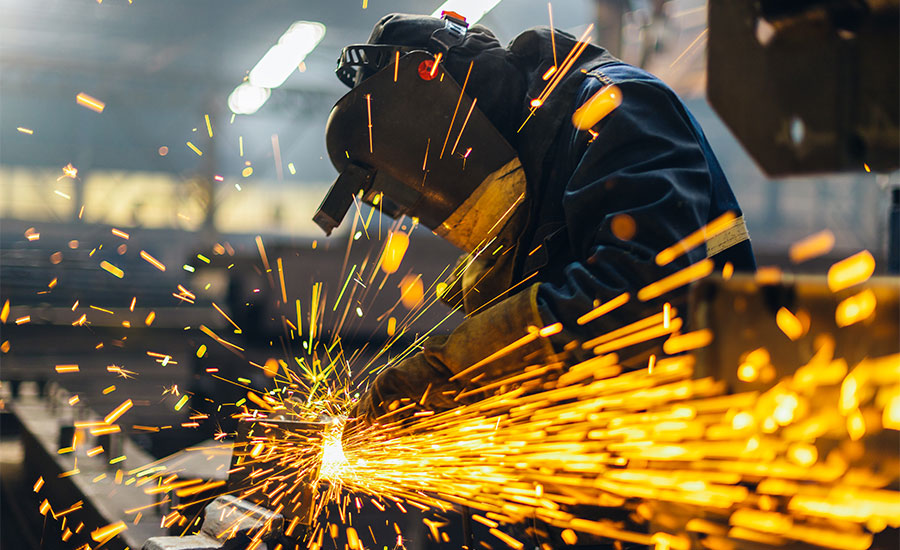

Essential Tools for Top Quality Welds
Understanding welding WPS requirements is necessary for welders to effectively make use of the necessary tools required for producing quality welds. The kind of welding machine needed depends on the welding procedure being utilized, such as MIG, TIG, or stick welding. Cable brushes and breaking hammers are crucial for cleaning the weld joint before and after welding to get rid of any type of impurities that might influence the top quality of the weld.
Key Methods for Welding Success
To attain welding success, one have to understand the essential techniques essential for generating high-grade welds. Preserving a stable hand and a stable welding position throughout the procedure is crucial to achieving accuracy and consistency in the welds. By mastering informative post these vital methods, welders can boost the high quality of their job and accomplish welding success.
Ensuring Conformity With WPS Requirements
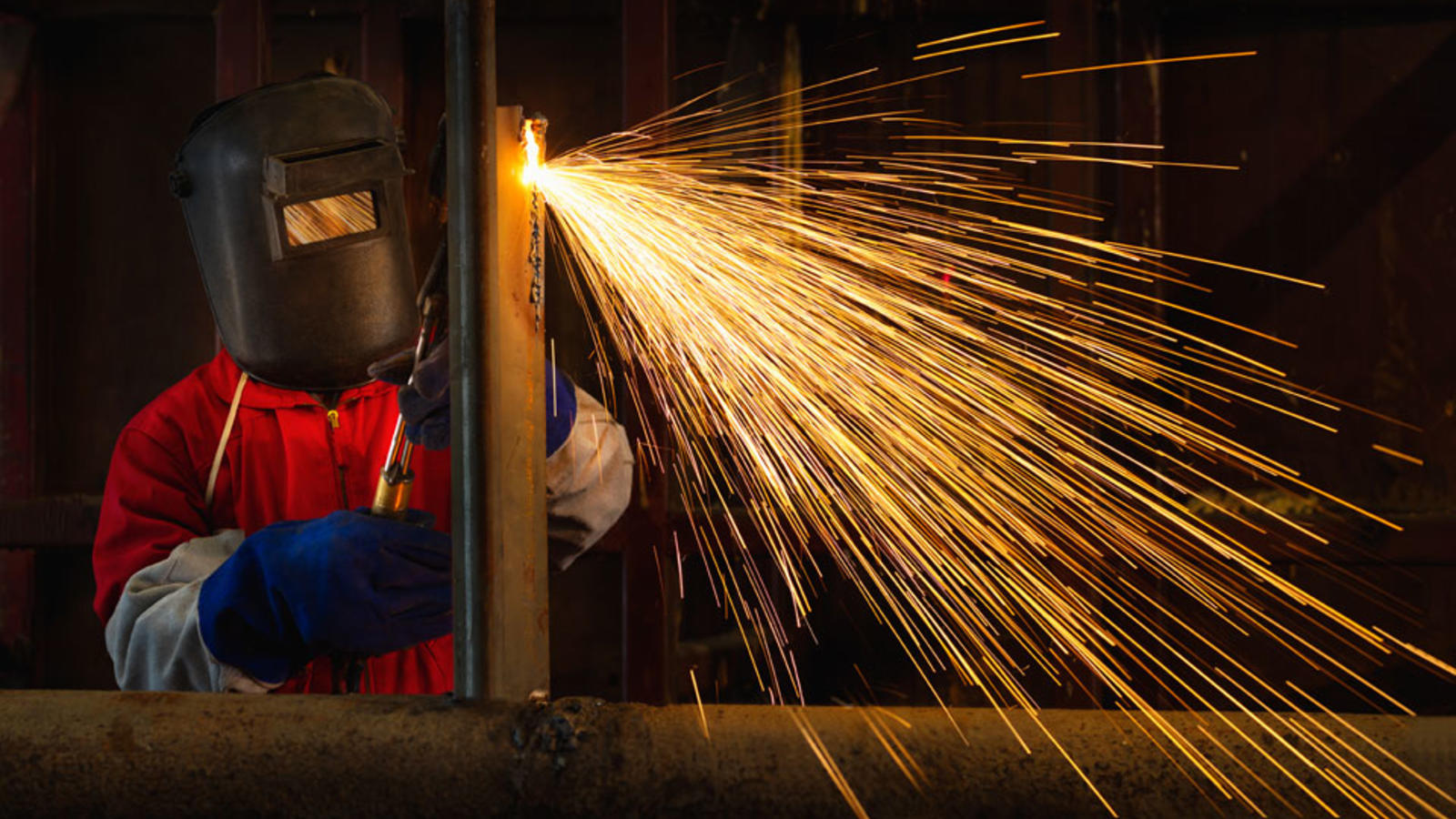
In addition, keeping comprehensive documents of welding specifications, devices calibration, and assessment results is vital for showing compliance with WPS standards. By carefully adhering to WPS requirements, welders can make certain that their work satisfies the required quality degrees and adds to the general success of the welding project.
Troubleshooting Common Welding Issues
When faced with usual welding problems, identifying the source is vital for reliable troubleshooting. One prevalent issue is the visibility of porosity in welds, usually caused by impurities such as oil, rust, or moisture. you could try this out To address this, making certain appropriate cleaning of the base steel before welding and using the right securing gas can dramatically lower porosity. Another issue frequently experienced is lack of combination, where the weld stops working to appropriately bond with the base click to read product. This can originate from poor warmth input or inappropriate welding technique. Adjusting parameters such as voltage, cable feed speed, or travel speed can help improve combination. Additionally, distortion, fracturing, and spatter prevail welding difficulties that can be minimized via proper joint preparation, consistent warm control, and choosing the ideal welding consumables. By extensively recognizing these common welding concerns and their origin, welders can effectively fix troubles and accomplish top notch welds.
Verdict
To conclude, understanding welding WPS standards needs an extensive understanding of the standards, utilizing important tools, and executing essential techniques for successful welds. Making certain compliance with WPS criteria is critical for creating high quality welds and preventing common welding issues. By adhering to ideal techniques and practices, welders can accomplish regular and trustworthy lead to their welding projects.
In the realm of welding, mastering Welding Procedure Spec (WPS) requirements is an essential component that directly affects the top quality and integrity of welds.When delving right into the world of welding methods, a crucial aspect to comprehend is the relevance and details of Welding Procedure Specification (WPS) requirements. WPS requirements give a comprehensive standard for welding operations, ensuring uniformity, top quality, and safety in the welding process. The kind of welding machine needed depends on the welding process being used, such as MIG, TIG, or stick welding.Accomplishing welding success with the proficiency of vital strategies demands a comprehensive understanding and adherence to Welding Treatment Requirements (WPS) standards.
Report this page